לאחרונה אנו עדים לעלייה בפופולאריות של סיבי פחמן. לא מדובר כאן בחומר גלם חדש או לא מוכר, אבל הירידה המתמדת בעלות שלו – בעיקר בזכות הקפי יצור מוגדלים ותהליכי הפקה יעילים יותר – גורמת לשלדות קרבון לסגור בהתמדה את פער המחיר ביחס לשלדות האלומיניום עתירות נפח היצור. הכתבה אמורה לתת לכם כלים בסיסיים בהבנת העולם המרתק הזה והיא מתייחסת בעיקר לעולם האופניים, אבל אפשר בקלות להשליך ממנה לתחום המוטורי ולתעופה.
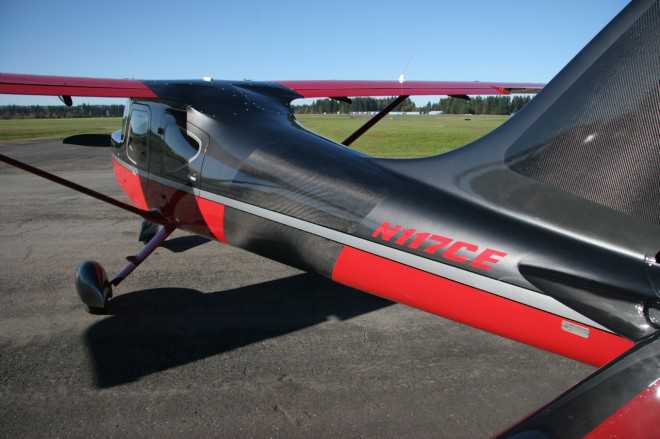
רוב רובו של הקרבון הגולמי והאיכותי מגיע מיצרנים ביפן: Toho Tenax, Toray Industrial ,Mitsubishi Rayon ואחרים. לכל יצרן יש קוד כך למשל קרבון של Toray יסומן כ-"T700" וכך הלאה.
שלושת הפרמטרים החשובים בקרבון הם: חוזק (עמידות בקריעה), גמישות ויכולת להימתח. אלו שלושת התכונות הבסיסיות של החומר כאשר יש איזון בין החוזק לגמישות – האחד בה על חשבון השני.
עוד מידע שיש לקחת בחשבון הוא מספר הסיבים בגדיל או TOW. זה יכול להיות 1,000 או 1K ויכול להגיע גם ל-60K (כמו Pinarello Dogma לכבישונים). בניגוד לסיב סינטטי, הגדילים של הקרבון אינם ארוגים – האריגה תחליש את תכונות החומר על ידי יצירת נקודות גזירה לאורכה.
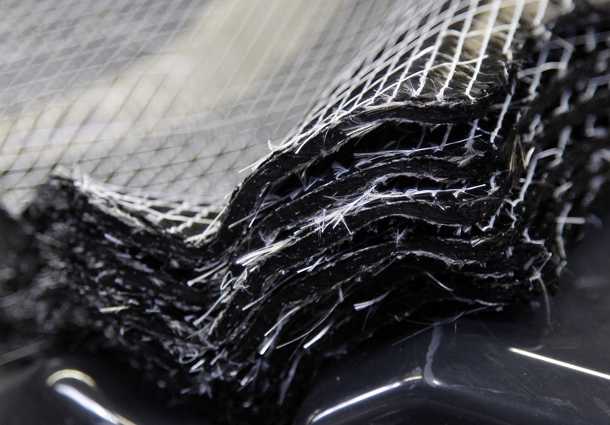
הגדילים האלו נארגים למשטחי בד במגוון עצום של אריגות. אלו יכולות להכיל גדילים גדולים או זעירים, אריגה צפופה מאד או מרווחת, דילוג על גדילים או ללא אריגה כלל אלא בקווים מקבילים. לכל סוג אריג השימוש הספציפי שלו בתלות בעומס שעל החלק לשאת או במורכבות המבנה שלו. למשקל האריג יש כאן חשיבות רבה וזה מופיע כגרם למטר.
יש אפשרות לרכוש את האריגים כשהם כבר מכילים את השרף או PREPREG. המשמעות היא כי שרף האפוקסי כבר נמצא באריג והוא מוכן להכנסה לתבנית. אבל איך למקם אותו? זו אחת השאלות המרכזיות בייצור חלקים ובעיקר שלדות מקרבון. באיזה סוג קרבון להשתמש? איזו אריגה? לאילו כיוונים, ביחס למעבר העומס ברכיב, יש לסדר את האריג? בכמה שרף אפוקסי להשתמש? מה צריך להיות היחס שבין כמות הקרבון לכמות השרף? ועוד.
באופניים
ראוי לציין כי רק אחוז מזערי מייצור הקרבון בעולם מגיע לייצור האופניים. ההערכות הן כי מדובר רק ב-5% – כשהצרכנית העיקרית של החומר היא תעשיית התעופה. בשל כך אין בנמצא קרבון גולמי או שרף אפוקסי אשר מיוצרים מראש בהתאמה לדרישות יצרני האופניים.
כמעט כל היצור של שלדות הקרבון באופניים נעשה בסין ובטאיוון על ידי קומץ מפעלים. אלו מפיקים שלדות על פי המפרטים והדרישות השונות של מותגי האופניים אשר משתפים פעולה עמם בתחומים של מחקר ופתרונות לדגמים השונים. לרוב שלדת אופניים תכיל כמה שכבות של אריג כשלכל שכבה תכונות פיזיות שונות, אריגה שונה, וכיוון אריג אחר. זאת, כדי לטפל בעומסים היחודיים לאופניים, לעמוד במכות מכאניות ולבסוף גם להגיע לגימור יפה. הסיבה שיש לשלב כיווני אריג שונים נעוצה בעובדה כי לקרבון עמידות רק על מישור האורך בעוד שהוא עשוי להגזר בקלות רבה על מישור הרוחב שלו. ובעצם האריג – שתי וערב – היפה שאתם רואים בשלדה שלכם נועד בעיקרו רק לצרכים קוסמטיים.

היצור נעשה על ידי תבניות שלתוכן מוכנס האריג בסדר שנקבע. אלו יכולים להיות צינורות ישרים או שלדות מונוקוק מורכבות. לתוך התבניות מוכנסים כיסי אוויר אשר מנופחים בלחץ רב וכל העסק הזה נכנס לאפיה באוטולאב – שזה תנור בלחץ וחום מאד גבוהים.
כשלים וזיופים
שמענו סיפורי זוועה על שלדות שנסדקו בתוך מכוניות חונות, על שברים מקפיצות גבוהות ועוד. רוב הכשלים נגרמים כשתהליך הייצור אינו מושלם ונותר אוויר כלוא בין שכבות האריג. קשה ליצור חלקים קטנים ומורכבים ולפעמים נותרי שיירים מתהליך היצור בתוך השלדה: שרף עודף, שקיות שנקרעו בחליצה ועוד. כל זה עשוי לגרום להיפרדות השכבות, לסדקים ולבסוף גם לכשל מוחלט. היום אנו נהנים מהדור הרביעי של שלדות הקרבון. אלו משתמשות בלחץ גבוה מאד בתהליך היצור – לחץ אשר דוחס מאד את השכבות ומבטל כל סיכוי לאוויר להיכלא בין השכבות, גם עודפי השרף נסחטים החוצה מהתבנית ואחוז הכשלים בייצור נמוך מ-4% (ראה כתבה על אופני PIVOT).
כמו עם מוצרים יקרים רבים אחרים גם כאן יש זיופים. וזיופים יכולים להיות שימוש בקרבון זול ולא מתאים ובתהליכי יצור מיושנים – וכמובן סימון השלדות בשם מותג יוקרתי. לאחרונה גם שמענו על סיבי זכוכית שנצבעו בשחור ושווקו כשלדות קרבון ממותגות. קשה מאד להבחין בעין בהבדלים למי שאינו בקיא אבל צריך לזכור רק שבסיבי זכוכית השרף אוחז את הסיבים ואת המבנה בעוד שבמבנה קרבון רוב השרף נסחט החוצה – יש לאריג "עומק" תלת-ממדי וטקסטורה.
בקרוב אצלנו
סיבי הפחמן הם זעירים – בין 5 ל-10 מיקרון בלבד – אשר מורכבים מאטומי פחמן המסודרים בשורות צפופות של גבישים על מישור האורך. זה מה שנותן את יחס החוזק/משקל המצויינים של החומר. החיסרון הוא שהחוזק הזה קיים רק בכיוון סידור הגבישים. העליה המתמדת בדרישה לחומר (עליה של כ-7% מדי שנה בשוק גלובאלי של כ-14 מיליארד דולר), בתעשיות התעופה, הבטחון, אנרגיה ירוקה ורכב, תמשיך את מגמת ההוזלה של החומר הקרבון אשר בבחטה נוטש את מחוזות האקזוטיקה היקרים לאיזורים נגישים יותר מהם כולנו יכולים ליהנות.